4. 工艺对材料体系要求
树脂体系
1. 树脂粘度要求合适:树脂体系的粘度≤300mPa∙s,粘度过大,成型大制品不易均匀布满模腔,灌注时间过长。
2. 固化放热峰温度低:放热峰温度过高,局部热量不易散出,易产生焦化。
3. 固化时间:适宜的固化时间,以便缩短工作周期
4. 物料性能:所选的树脂应具有较好的力学性能,拉伸强度和弯曲强度要高,耐腐蚀性能好,固化收缩小,同时符合GL认证的要求。
5. 价格便宜,来源广泛,无毒。
增强材料体系
(2)导流介质的使用比例对树脂充模速度的影响
增强材料体系
1. 树脂的流动阻力小,树脂浸润性好。
2. 机械强度高,符合GL认证的要求。
3. 铺覆性好,即增强材料在无褶皱,无断裂、不撕裂的情况
下能够容易与工件随行。
4. 质量均匀性好。 5. 真空灌注成型工艺的影响因素
原材料
1. 增强材料(最终反映在渗透率上)
(1) 树脂流通通道树脂在纤维中的流动通道有两种,一种是纤维束与纤维束之间的孔隙A(纤维编织方式如右图),另外一种是纤维束纤维丝之间的孔隙B(纤维直径)。
(2)纤维表面助剂表面助剂的一个重要功效就是增加纤维与树脂浸润能力,这在灌注工艺中尤为重要,使得树脂能快速浸入并流过纤维铺层。
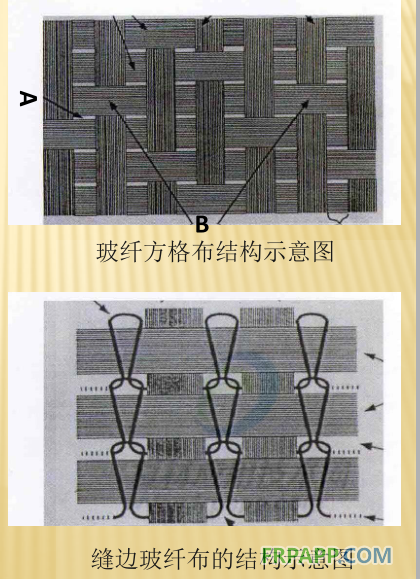
2. 树脂
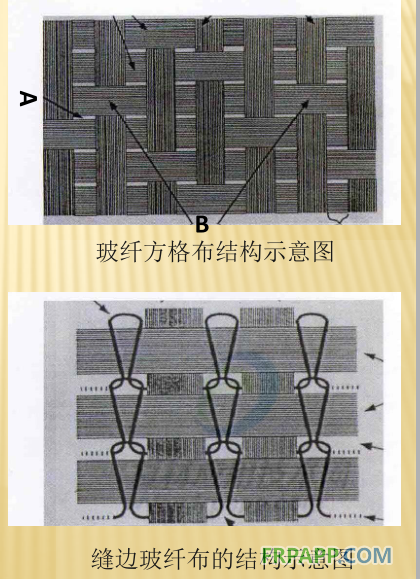
2. 树脂
(1)树脂粘度
由达西定律可知,树脂的粘度对灌注速度有明显的影响,粘度越大,灌注速度越小,同时大粘度的树脂中夹带的气泡不易除尽,会影响最终叶片的质量。
(2)控制树脂凝胶时间
树脂凝胶时间应该适当,过短会导致叶片没有完全灌注即凝胶。过长会导致叶片缺胶。
3、导流介质
3、导流介质
真空灌注成型工艺中导流介质的引入,使这种工艺应用于大型复杂结构复合材料制品成为可能。它可以大幅度提高树脂的灌注速度。
(1)导流介质的铺放方式对树脂充模时间的影响

从图,树脂的充模时间随导流介质使用比例的增加而呈线性减少,因此在工艺控制时,可以通过改变导流介质的使用比例实现对树脂充模时间和充模过程的控制 。
(3)导流介质对预成型体上下表面树脂流动前沿差距的影响
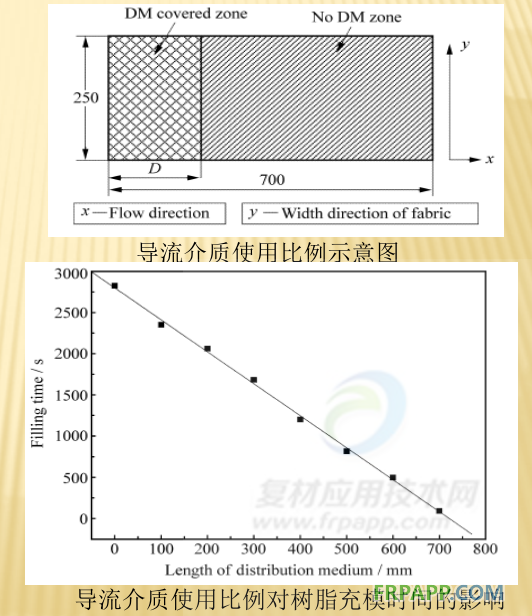
(3)导流介质对预成型体上下表面树脂流动前沿差距的影响
导流介质的引入可以提高树脂的流动速度,同时也会导致铺层上下表面浸润差距的产生。浸润面差距过大则会对整个工艺效果产生影响。因此铺设导流网时需要控制导流介质的使用比例。
管路布置
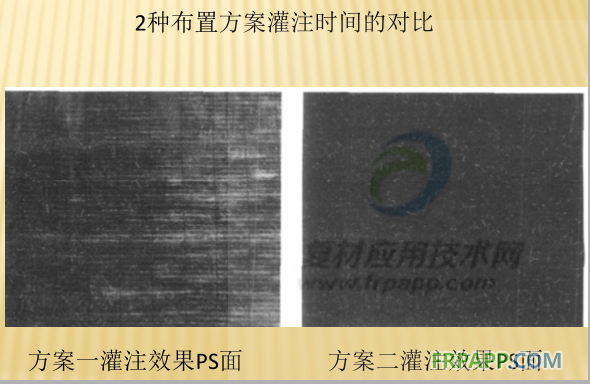
管路布置
合理的抽气管路和进胶管路的布置有利于提高灌注质量和缩短灌注时间。
布管的原则:以不产生包围为前提,尽可能的最小化树脂的流动距离。
不同的布管方式对灌注时间和灌注质量的影响见下图表2。
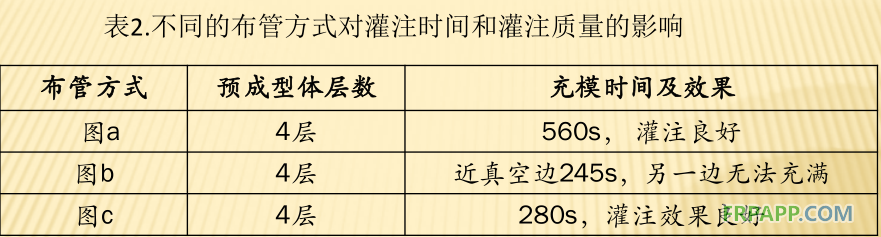
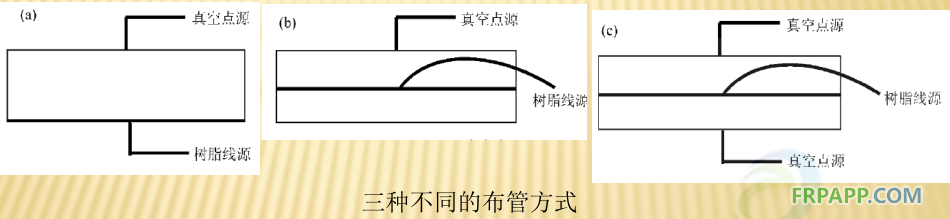
因此,要获得较快且均匀的充模,树脂源应置于模腔的几何中心,以尽量缩短树脂的流动距离,而且树脂源与真空源尽可能对称,平衡布置,以避免干点的产生。
对于复杂的制件,如叶片,可以根据制件的形状和不同部位增强层的厚度,适当引入多个树脂源。(下图是叶片两种布管工艺)
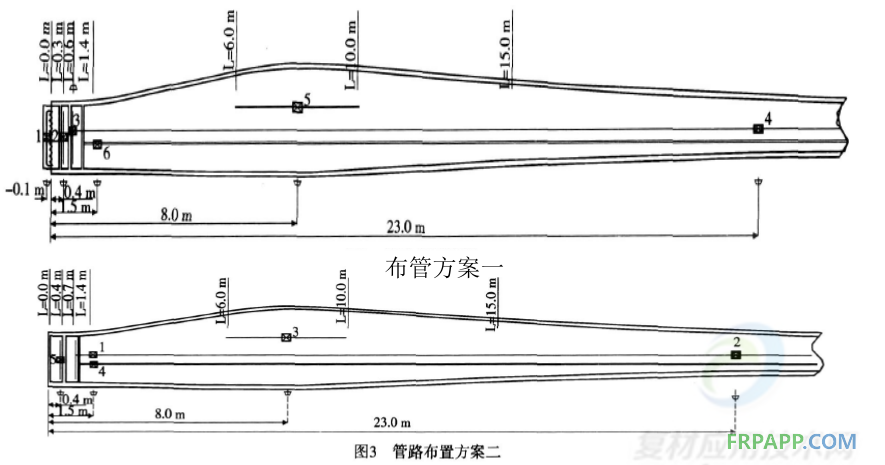
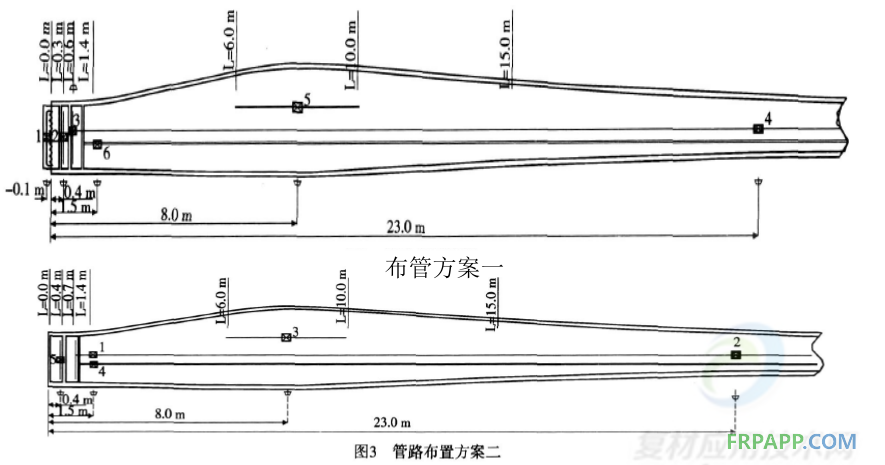
从料种布管方案的灌注时间和灌注效果来看,方案二的布管方案有明显优于方案一。 方案一中树脂由叶根向叶尖流动,距离真空源较远,气泡不容易排出所导致。
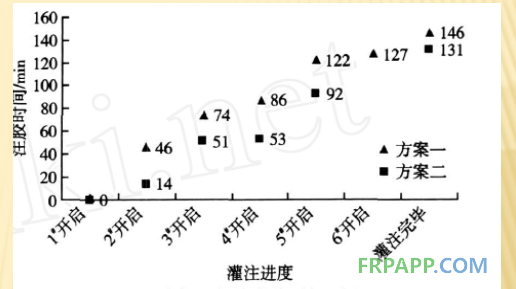
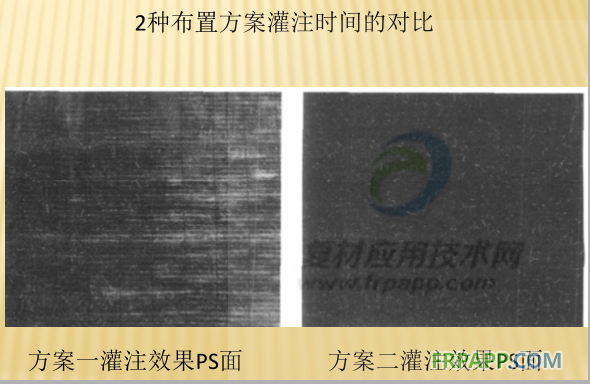
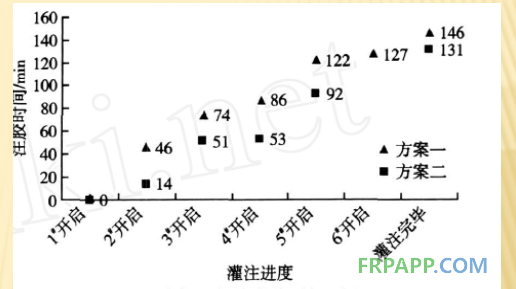
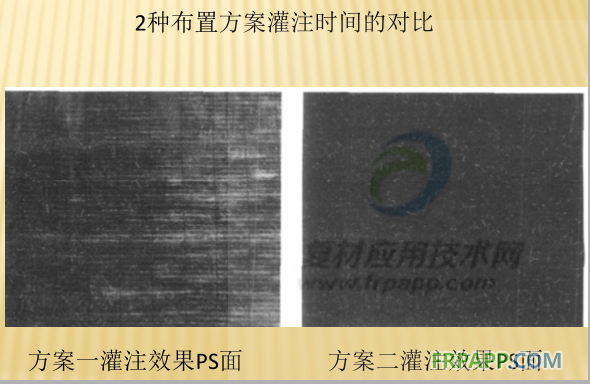
真空体系
真空体系是由模具、真空袋膜和密封胶密封构建而成。真空灌注几乎最重要的工艺参数就是系统和模具的抽真空质量。最小的漏气也会导致空气被吸入铺层,铺层内的压力梯度能很快催生气泡并散布开来,最终带来成品的缺陷。(如发白)
温度
在叶片进行真空灌注的过程中,温度也是一个重要的因素,作业环境的温度、灌注树脂的温度及模具及模具上纤维的温度都会直接影响到灌注的速度,因为树脂的粘度会随温度的增加而减少,粘度降低,树脂在纤维中流中的速度也加快
6. 叶片的真空灌注成型工艺
6. 叶片的真空灌注成型工艺
叶片成型工艺中常用的主材
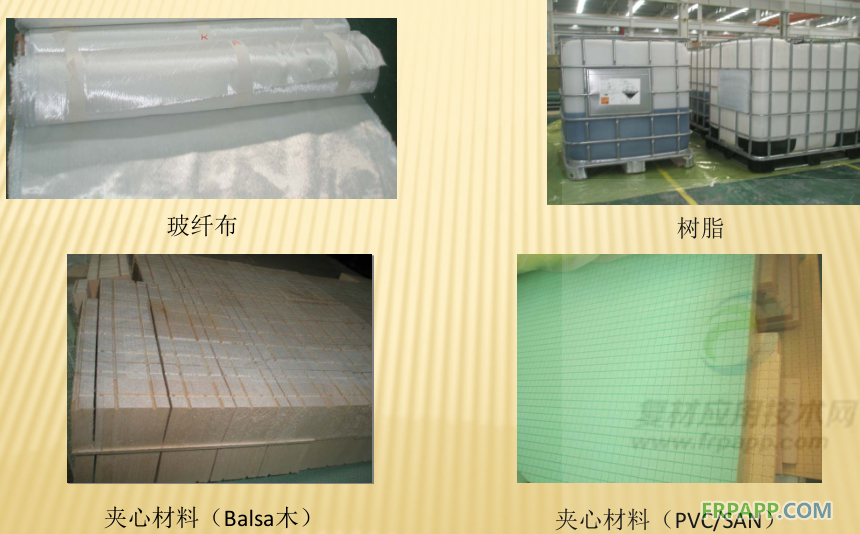
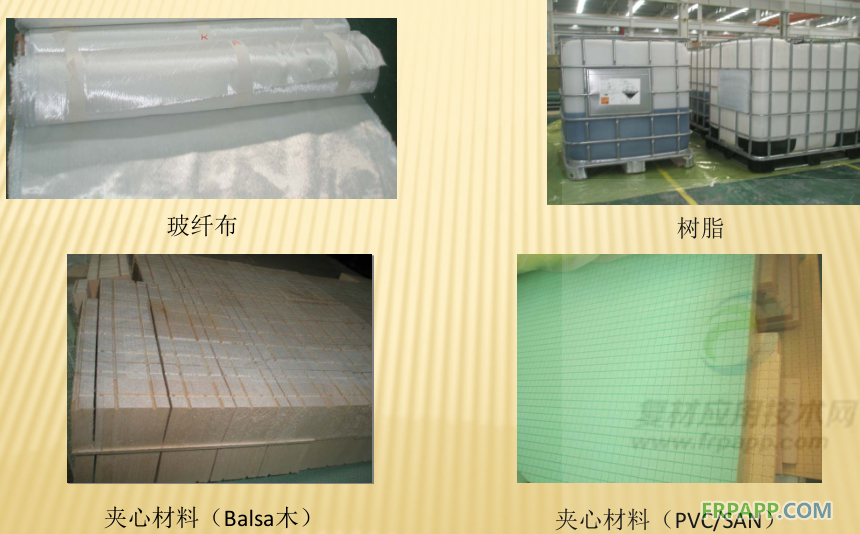
叶片成型工艺中常用的辅助材料

叶片成型工艺具体的流程
1. 模具准备
模具加热系统的检查和模具的清洁
2. 打脱模剂
沿着一个方向均匀涂敷一层脱模剂
3. 铺放脱模布和表面毡
提供一个清洁,富树脂层,粗燥的表面,便于后续的打磨和喷漆工序
4. 铺放增强材料和夹芯材料
必须确保增强材料平、顺、直,没有褶皱,随型
5. 铺放脱模布和导流介质
脱模布和导流介质的配合使用可以提高树脂的流动速度,减少叶片的灌注时间,同时脱模布的铺设便于叶片与辅助材料的分离
6. 进胶管路的铺设
进胶管路的铺设原则是在保证不发生包围的情况下,尽量使树脂灌注时间最短(叶片壳体中常见的两种布管方式)方案一的灌注时间明显小于方案二的灌注时间(见下图)


7. 抽气管路的布置
抽气管路布置在叶片的四周,根部区域抽气口应布局的相对多一些
8. 真空体系的构建
采用真空袋膜和密封胶构建真空系统,提供密封体系
9. 检漏保压
关闭抽气阀门保压。15min后,要求压力损失不大于0.004MPa。必须确保整个真空体系不漏气.
10. 树脂的灌注
灌注时注意进胶口的开管顺序,防止出现包围的现象
11. 预固化
加热加速树脂的固化,同时放置树脂放热而导致温度过高
12. 后固化
确保树脂固化完全。
八、总结
八、总结
RTM 工艺以它友善的工作环境,优异的力学性能使得它在未来的中国玻璃钢发展中,逐渐取代手糊等落后的工艺,成为一种主流的玻璃钢生产工艺, , 但是也应该注意, , 只有努力改善应用和对相应的员工进行培训,才能真正让这项先进的工艺为之所用 。
我们可以利用该工艺的诸多优点来作为基础,多开发一些高附加值的产品,如汽车轻量方面的,新能源方面的,碳纤制品等等,提升本公司的产品的竞争力,努力去开拓市场,以此来给本公带来新的经济增长点,同时也健康良性带动了 RTM