海洋是资源和能源的宝库,尤其是深海领域,蕴藏着丰富的大洋矿物资源和生物资源。在陆地资源日益枯竭的情形下,向海洋开发已成为必然的趋势。目前,深海勘探、开发主要以深潜技术为基础,利用潜器、水下机器人等进行水下作业。高强度固体浮力材料是现代深潜技术的重要组成部分之一,对保证潜器的浮力,增大潜器的有效载荷,减少其外型尺寸等具有重要作用。
目前,国内外生产的深海高强度固体浮力材料主要是用空心玻璃微珠填充聚合物制成的。空心玻璃微珠是一种无机非金属空心球形微粉新材料,具有粒度小、球形、质轻、绝热、隔音、高分散、耐高低温、耐腐蚀、压缩强度高、电绝缘性和热稳定性好等其它轻质填料所无法比拟的优点[5,6]。它是一种优良的无机填充材料,能够在强度降低不大的情况下有效的降低材料的密度,被广泛的应用于建材、塑料、橡胶、涂料、海底探测、航海和航天等国防和民用领域中,其应用越来越受到人们的关注,并且已成为材料科学研究的热点之一。固体浮力材料所用的聚合物一般是环氧树脂,将大量的空心玻璃微珠 填充到环氧树脂中,复合成轻质浮力材料,在深海中可承受高压,并且保持较小的吸水率。
作为深潜用固体浮力材料,材料性能的均一性对深潜器的安全和配重平衡有很大的影响。本文将牌号为K20和HGS8000X的两种具有不同粒径和不同密度的空心玻璃微珠以不同的体积比填充到环氧树脂中制成复合材料,详细研究了微珠的体积比对复合材料密度、压缩强度等性能均一性的影响,并讨论了造成均一性不同的原因。
2. 实验
2.1. 实验主要原料
为了使实验结果能够直接适用于指导实际生产,本实验所采用的主要原料均为市场上易于采购的商 业试剂或工业原料,详细情况如表1。
2.2. 试样制备
模具及处理:复合材料采用实验室自制的Φ160 × 140 mm的圆筒形不锈钢模具制备。将模具提前装 好,并在模具内腔均匀的涂一层脱模剂,置于80℃的干燥箱中预热,备用。
混料过程:将一定量的环氧树脂、十二烯基琥珀酸酐、甲基四氢苯酐、KH-560 和 N,N-二甲基苄胺分别加入到不锈钢桶内,搅拌均匀。然后再加入不同体积比的空心玻璃微珠,搅拌至微珠被环氧体系完 全浸润。空心玻璃微珠的总体积约占物料总体积的60%,K20的体积占微珠总体积分别为0%、10%、20%、50%、80%、90%、100%。将容器置于真空搅拌器内进行真空搅拌30分钟。
注模固化过程:将混合好的物料注入已经备好的模具内,注入量以冷却脱模后材料的高度9 cm~10 cm 为标准,加压至2 MPa。将模具置于165℃的干燥箱内固化6 h,冷却后脱模。
2.3. 性能测试
制样及测试过程:用精密切割机将复合材料切成尺寸为10 mm × 10 mm × 20 mm的长方体试样,排 水法测其密度,按照GB/T 2567-2008进行压缩强度的测试。
取样方法:为了分析材料性能的均一性,沿着加压方向分三层取样如图1所示。
3. 结果与讨论
3.1. 微珠配比对复合材料密度的影响
实验采用了粒径较大的 K20 和粒径较小的 HGS8000X 按不同的配比制备了复合材料。对单独采用K20和HGS8000X所制备的浮力材料计算分析,其中的空心玻璃微珠的填充率(空心玻璃微珠在复合材料中的体积分数)为 61%。假设将两种微珠按不同配比混合后所制备的复合材料中玻璃微珠的填充率均为61%,则混合微珠复合材料的密度(视为理论密度)应为:
珠K20和HGS8000X的密度,ρe为固化环氧树脂的密度(本实验采用环氧体系的密度为1.1 g/cm3)。理论密度与测得材料的密度随K20体积分数的变化规律如图2所示。从图中可以看出,复合材料的密度随K20体积分数的增加而降低,其降低趋势与理论密度的降低趋势一致。同一试样中,中间层的密度普遍低于 上层和下层材料的密度。同时也可以发现,单独采用K20或HGS8000X所制备的复合材料的密度与理论密度比较接近,而两种不同粒径的微珠混合所制备的复合材料密度均不同程度的低于理论密度。此外,复合材料上、中、下三部分的密度有一定的差值,即材料上、中、下三部分的密度表现出一定程度的不均一性。随着 K20 体积分数的变化,复合材料的这种不均一性也发生相应的变化。从复合材料上、中、下三部分密度的方差图(图 2 右上插图)可以看出,随着 K20 体积分数的增加,方差值开始逐渐变小,并在某一点处达到最小值,当 K20体积分数继续增加时,方差值又开始变大。说明随着K20体积分数的逐 渐增加,复合材料密度的均一性先变好,后变差,并且在中间某个值处均一性达到最好。可见,两种不同粒径的空心玻璃微珠混合所制备的复合材料,其密度均一性较单一空心玻璃微珠制备的材料好;而且,采用粒径较大的微珠制备的复合材料比粒径较小的微珠制备的材料密度均一性好。
3.1. 微珠配比对复合材料压缩强度的影响
图 3 是两种不同粒径空心玻璃微珠按照不同的体积分数所制备的复合材料上、中、下三部分的压缩强度随微珠配比的变化曲线。从图 3 可以看出,与复合材料的密度随玻璃微珠配比的变化规律相似,复合材料上、中、下三部分的压缩强度也随K20体积分数的增加而降低,这一趋势是由K20本身的强度较低所导致。另外,同一微珠配比的复合材料其上、中、下三部分的压缩强度也表现出一定程度的不同,即材料的压缩强度也有一定程度的不均一性。从压缩强度方差分析结果(图3右上插图)可以看出,两端的方差值均大于中间值,尤其是单独采用粒径较小的HGS8000X制备的材料,其方差值远大于其它复合材料,除此之外,其它材料试样上、中、下三部分的压缩强度方差均比较小。说明除单独采用粒径较小的微珠制备的复合材料外,其余所有材料的压缩强度均一性都较好。
3.2. 复合材料结构分析
材料的性能取决于材料的组成与结构,本实验采用了确定的环氧体系和确定的空心玻璃微珠,所以
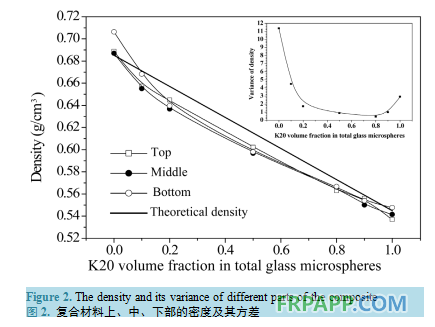
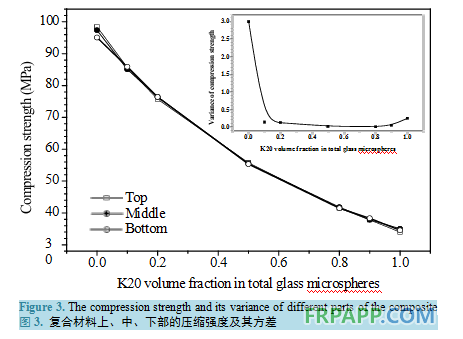
其性能将主要取决于材料的结构。对材料的显微结构分析结果发现,在微珠配比确定的情况下,材料上、 中、下层的显微结构没有明显的区别,而当微珠配比发生变化时,材料中玻璃微珠粒径的分布发生了明显的变化。取 K20体积分数为0%、50%和100%的三种材料上、中、下层的试样作为典型的显微结构(如图 4)。从图中可以看出,三种配比的复合材料均具有良好的结构致密性,除空心玻璃微珠所营造的空间外,几乎没有明显的空隙。K20体积分数为0%的复合材料中,最小微珠直径为10 μm左右,而最大微珠 直径也仅有35 μm左右;K20体积分数为100%的复合材料中,最小微珠直径约为 20 μm,而最大微珠直径接近100 μm左右;K20体积分数为50%的复合材料中,微珠的直径从10 μm到100 μm左右分布。以 上分析可以推断,对同一微珠配比的试样,其上、中、下层的密度和压缩强度产生不均一性的主要原因应该是材料固化过程中压力分布不均匀。在固化过程中,压力分布不均匀引起材料上、中、下层所产生的残余应力不同,当材料脱模时,在不同应力的作用下,材料所产生的回弹程度不同,从而造成材料产生较小的性能偏差。当采用密度较小的微珠不同程度地替换密度较大的微珠时,复合材料密度的降低与 理论计算的结果有较大的偏离(如图2),其主要原因是不同比例微珠的复合导致微珠的粒径分布发生了变化。从图4中不难看出,当两种不同直径的空心玻璃微珠混合时,微珠的直径集中分布在约以20 μm为中心和以60 μm为中心的两个范围内,呈现出典型的双峰分布趋势,这种分布使其堆积密度得到较大的 提高。对复合材料内部微珠堆积系数的分析结果如图 5 所示,混合微珠的堆积系数明显高于单一微珠。
由于微珠堆积系数的提高,使混合微珠制备的复合材料密度低于理论计算的密度。所以,采用不同直径的微珠混合制备复合材料是降低材料密度的有效手段。另外,对比图 5 不难发现微珠的堆积系数越高, 所制备的复合材料的性能均一性也越好。
4. 结论
1) 由两种不同直径的空心玻璃微珠混合所制备的复合材料,其密度、压缩强度的均一性优于单一组分微珠制备的材料。
2) 不同直径的空心玻璃微珠混合填充,是降低复合材料密度的有效手段。
3) 空心玻璃微珠的堆积系数越大,复合材料的性能均一性越好。