环氧代木加工后先喷涂一层过渡层,将环氧树脂封闭。
彻底解决问题,即使施工环境较差,也不影响粘接。
除了提高粘接,还对环氧树脂有效封闭。
方便施工、快速干燥。
不单独销售,免费配套提供给环氧代木的客户。
原模用手糊及导入环氧树脂系统料
相对环氧代木,原模用手糊及导入环氧树脂系统料,技术难度较低。
一般配套销售,仅开发树脂而无环氧代木客户难接受。
环氧代木开发完成,获得配套优势。
独特的固化剂体系,保证常温较长的适用期的前提下,具有较好的常温固化度。
以原模材料带动成品模具材料
开发适合导入和手糊工艺的阴模环氧树脂系统料。
针对客户需求,快速响应。
对产品性能进行细分,针对不同应用场景开发不同产品。
导入工艺:常温混合粘度300mPa.s左右,凝胶时间2-3小时左右。
手糊工艺:常温混合粘度600mPa.s左右,凝胶时间1小时左右,常温固化后具有较高固化度。
牌号 |
工艺 |
粘度 |
Tg |
凝胶时间 |
INV-E706/C706 |
环氧代木 |
/ |
65℃ |
/ |
INV-E720/C720 |
手糊 |
600 |
80 ℃ |
60-90 |
INV-E721/C721 |
手糊 |
600 |
125 ℃ |
50-70 |
INV-E741/C741 |
导入 |
350 |
120 ℃ |
130-200 |
INV-E742/C742 |
导入 |
400 |
160 ℃ |
130-200 |
INV-E743/C743 |
导入 |
400 |
180 ℃ |
130-200 |
树脂名称 |
不同后固化温度下的Tg |
|||
80℃ |
120℃ |
140℃ |
150℃ |
|
某进口树脂 |
105 |
125 |
130 |
135 |
INV-E740/C740 |
105 |
112 |
113 |
113 |
INV-E741/C741 |
105 |
125 |
126 |
128 |
INV-E742/C742 |
105 |
135 |
155 |
160 |
树脂名称 |
不同后固化温度下的固化度排序 |
|||
80℃ |
120℃ |
140℃ |
150℃ |
|
某进口树脂 |
3 |
2 |
2 |
1 |
INV-E740/C740 |
1 |
1 |
1 |
1 |
INV-E741/C741 |
2 |
1 |
1 |
1 |
INV-E742/C742 |
4 |
3 |
2 |
1 |
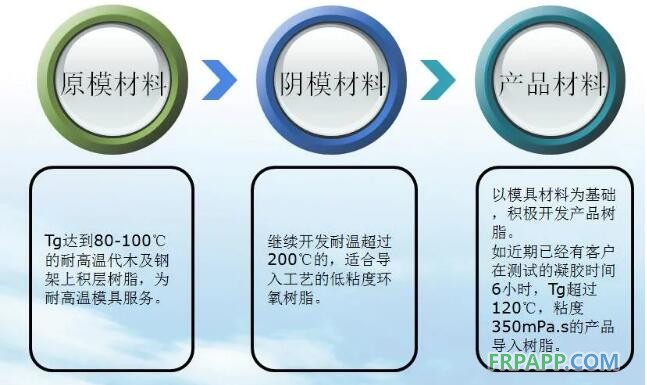
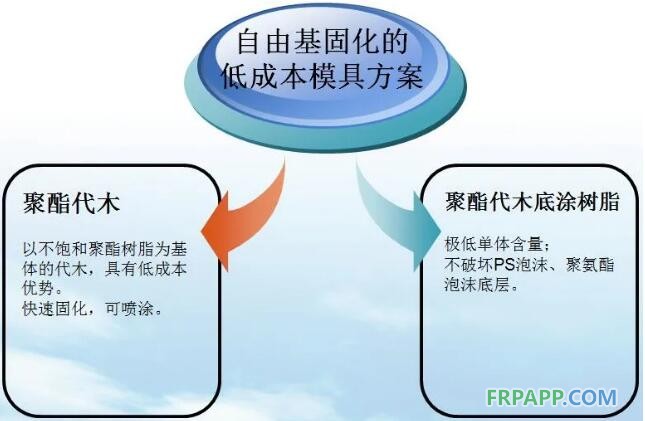